Practice of antibacterial and deodorant finishing of fabric
Practice of antibacterial and deodorant finishing of fabric
Abstract: This paper summarizes the development, production and application of antibacterial and deodorant finishing agents, introduces the production methods of antibacterial textiles, and focuses on the application process of modified chitinous antibacterial and deodorant finishing agents. The AATCC100 standard test proves Herst ATB antibacterial finishing textiles. Highly effective and durable antibacterial and deodorizing effect, and Herst ATB is low cost, safe and environmentally friendly, suitable for industrial production
' Functional finishing
Antibacterial and deodorant finishing agent
Microorganisms have seriously affected human life, and pathogenic microorganisms have caused great harm to the human body. Antibacterial finishing of fabrics is one of the ways people can eliminate these pathogenic microorganisms. Antibacterial finishing is called antimicrobial finishing in the United States, etc.; it is called antibacterial and deodorizing processing in Japan; it is called hygienic finishing in China. Textile antibacterial agents can be divided into three major categories: natural, organic and inorganic. Each type of antibacterial agent has its own advantages and disadvantages. The organic antibacterial agent has good effect and many varieties. It is the most widely used antibacterial agent at present, but it has problems such as poor high temperature stability and is difficult to be used in synthetic fiber spinning process; Antibacterial agents usually have good safety, but their application range is narrow, most of them seriously affect the color shade of fabrics; inorganic antibacterial agents have good heat resistance, but it is difficult to obtain durable effects for textile finishing, and most varieties have heavy metals. Toxic problem.
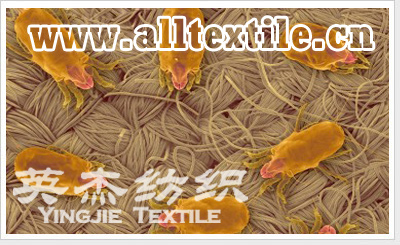
Organic antibacterial finishing agent
Organic antibacterial finishing agents can be divided into two major categories, namely, dissolution type and non-dissolution type. The dissolution-type antibacterial finish is not chemically combined with the fabric and can therefore be carried away by contact with water. Such antibacterial finishes are mainly used on disposable textiles (disposable textiles). Common dissolution-type antibacterial agents are: aldehydes, phenols, alcohols, certain surfactants (such as quaternary ammonium salts), organic heterocyclic compounds (such as pyrazoles, pyrimidines, pyrrole), organic metals Compounds (such as organic mercury compounds, organic copper compounds, organozinc compounds, organic lead compounds, organotin compounds, and some other organometallic compounds). Since such antibacterial agents are detached upon washing, they cannot be used for textiles that require multiple washings and have a long-lasting effect. The non-dissolving antibacterial finish can be chemically bonded to the fabric, and the finish treated fabric is durable for wearing and repeated washing. The method comprises the steps of grafting or polymerizing an antibacterial agent on the fiber or mixing an antibacterial agent into the spinning dope to achieve controlled release of the active material for durability. The non-dissolving antibacterial agent and the fiber are combined by a strong chemical bond, on the one hand, the agent cannot enter the cells of the microorganism, has no influence on the nucleus (genetic factor), and does not appear to be resistant to the bacteria; on the other hand, the antibacterial agent is not The secretions of the human body are absorbed into the human body and have high safety performance for the human body and the environment. Therefore, in addition to certain specific uses, the non-dissolving type has completely replaced the dissolution-type antibacterial finishing agent. The commonly used non-dissolving antibacterial finishing agents mainly include: silicone-quaternary ammonium salts, diphenyl ethers, organic nitrogens, nitrofurans, biguanides, chlorobenzimidazoles and the like.
Inorganic antibacterial finishing agent
The inorganic antibacterial agent is an inorganic substance such as an antibacterial metal ion and a composite thereof with an inorganic carrier. It has the advantages of good heat resistance and processing. It can be widely used in plastics, synthetic fibers, building materials, paper making and other fatty acid methyl ester ethoxylates (FMEE), which is an emerging non-ionic surfactant in recent years, with unparalleled low foaming, The functions of emulsification, dispersing and washing have been widely used in foreign countries, and the scouring pretreatment process in the textile field, especially the fabric, has been successfully applied. FMEE is an 18-carbon fatty acid methyl ester attached to a different EO number of ethylene oxide because the fatty acid methyl ester has an ester-like molecular structure similar to that of fats and waxes. According to a similar mechanism of solubility, the fatty acid methyl ester ethoxylate It is the best degreasing and dewaxing product among various surfactants. According to the article published in the International Washing Standards by Dr. Tom Senwelo of the American Washing Association, the degreasing ability of fatty acid methyl ester ethoxylate FMEE It is 1.5 times that of fatty alcohol polyoxyethylene ether and 2.5 times that of triethanolamine oleic acid soap. In terms of wax removal, FMEE has a wax removal capacity of 1.6 times that of fatty alcohol polyoxyethylene ether and 1.4 times that of triethanolamine oleic acid soap.
Has the following characteristics:
It has an ester group in the molecular formula, similar to grease and waxy structure, and has strong ability to dissolve and remove oil, mineral oil and paraffin according to the principle of similar compatibility.
The cloud point is greater than 100 ° C. Since the nonionic surfactant has the best performance at the temperature near the cloud point, the foam point has the lowest foam performance and the highest cleansing ability. FMEE can be used directly in high temperature process conditions.
It has strong dispersing performance, can disperse oil, wax, dirt and the like in the working fluid to prevent anti-staining. Therefore, it is also suitable for degreasing and wax removal under low temperature conditions, and compensates for the low dispersion of working fluid due to low temperature.
Application in the field of printing and dyeing:
, knitwear scouring agent
At present, the AEO series is commonly used in pre-knit processing. AEO has a large defect in poor dispersibility, and in the small bath ratio working solution, due to the anti-staining of impurities such as oil, the refining effect is deteriorated, and the uneven effect is uneven. FMEE has excellent degreasing performance, low foaming and good dispersibility. It is especially suitable for batch pretreatment of knitted fabrics. The cleaning effect is obviously better than that of fatty alcohol ether series.
, chemical fiber low temperature degreaser
Because FMEE has excellent dispersing and cleaning performance, it has excellent degreasing performance under low temperature conditions. It is suitable for low temperature and normal temperature degreasing of polyester fiber, spandex and other chemical fiber fabrics, and can realize direct dyeing process without liquid discharge.
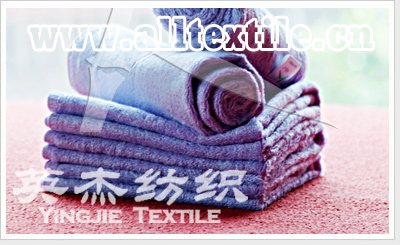
, cotton fiber wax remover
As the price of cotton is high, the quality of the yarn and the pulp used is getting worse and worse, which leads to the problem of unclean cotton wax removal. FMEE removes the cotton wax thoroughly and can be used as a fabric wax remover. Eliminate the surface wax and wax spots. Like all nonionic products, FMEE has poor alkali resistance. In order to improve its alkali resistance, FMEE is sulfonated to obtain its anionic sulfonate, FMES. FMES inherits the characteristics of FMEE high-efficiency degreasing and wax removal. It has high alkali resistance after sulfonation. FMES can withstand 50g/L for 100°C hot alkali and 150g/L for 40°C hot alkali. FMES is suitable for the strong alkali desizing and scouring pretreatment process of woven fabrics. The pretreatment of woven fabrics is an old topic. It seems that there is no new idea, but as the pretreatment process becomes shorter and shorter, and people expect the use of caustic soda. Less and less, the pre-treatment of woven fabrics has become a new challenge. The current woven pretreatment agents are mostly nonionic fatty alcohol ethers (AEO, TX, isomeric alcohol ether) and anions (sodium secondary alkyl sulfonate SAS, sodium dodecyl benzene sulfonate LAS), etc. In order to improve its alkali resistance, the phosphate ester product continues to be compounded. Among the above raw materials, the wax removal performance of the fatty alcohol ether is far from sufficient, and the removal of the slurry is not thorough, especially in the groove or the water washing tank, causing the slurry to coagulate and decontaminate. Sodium secondary alkyl sulfonate has good permeability due to its small molecular weight, but its cleansing performance is particularly poor. LAS is cheap but has a high foam, poor hard water resistance and high water quality requirements. Compared with the above raw materials, FMES is a comprehensive and refined raw material, such as excellent alkali resistance, so there is no need to compound phosphate ester products, and phosphate ester products such as OEP have very poor cleansing power. effect. The biggest advantage of FMES is that it has high desizing rate for various slurries and thorough removal of cotton wax, which can effectively prevent the agglomeration of slurry and other impurities in the rolling tank and the washing tank. Therefore, FMES has many advantages such as low foaming, alkali resistance, high desizing rate, high wool effect, etc., and is especially suitable for the woven fabric pretreatment process.
Production status with FMES:
The main raw material used is methyl 18-carbon stearate, which is the first cracking product of petroleum. Therefore, the production of FMEE in the world is mainly concentrated in petrochemical companies such as Xihe Petroleum, Bitei Petroleum and Murphy Petroleum. The output of Xihe Oil is the largest. The addition reaction of fatty acid methyl ester with ethylene oxide is complicated, the catalyst efficiency is low, the reaction time is long, especially the conversion rate of the target product is low, and the domestic catalytic and synthetic processes have made unremitting efforts, but the key catalytic process has never broken. The obtained product is of poor purity and has not been industrialized so far. The author believes that this situation is caused by the fact that China's entire chemical system is in a backward state compared with foreign countries. From oil refining to final formation of fine products, there are many links in the middle, each link is a little bit worse, and the gaps in all links are accumulated. This has caused this situation. The vast ocean is the cradle of life and the treasure house of resources. The minimum growth inhibition of mold is 10-20 mg/kg. According to electron microscopy, the morphological changes of bacteria after Herst SAL occurred: Gram-positive bacteria such as Staphylococcus aureus cell wall thinning and damage, replication was inhibited; Gram-negative bacteria such as Escherichia coli cytoplasmic concentration The gap is obviously enlarged. Herst ATB is a chitosan derivative which exhibits a very high antibacterial property due to the introduction of a highly antibacterial active group which greatly increases the killing rate. SGS, ITS, Japan Textile Inspection Association, Japan Chemical Fiber Inspection Association, China Center for Disease Control and other authoritative units have proved that antibacterial agents Herst ATB and SAL antibacterial finishing fabric can effectively kill MRSA and Staphylococcus aureus in contact with fabrics. Escherichia coli, Klebsiella pneumoniae, Pseudomonas aeruginosa, Bacillus subtilis, Candida albicans, Fusarium oxysporum, Aspergillus niger and other harmful bacteria, the antibacterial rate against Staphylococcus aureus after washing 60 times still reached more than 99.9%; No irritation to the skin, no toxicity to the human body, no teratogenicity, no mutagenicity, no potential carcinogenicity, no harmful substances such as formaldehyde, heavy metal ions and aromatic amine compounds, meet environmental protection requirements, and prevent sweat odor Skin itching has a significant effect.
Experimental Materials
Experimental cloth: cotton poplin JC40×40 110×90 270 cm experimental drug: antibacterial agent Herst ATB, provided by Herst International Group
Process flow
Grey cloth! Seam! Singeing! Desizing! Cook! bleach! dyeing! drying! Dip the antibacterial solution! Tension
Pretreatment
The pretreatment process uses conventional processes to achieve the quality requirements of normal printing and dyeing semi-finished products. The singeing effect is 3 to 4 grades, the whiteness is above 80%, and the gross effect (30 min) is required to be 8 cm or more.
Antibacterial finishing process
Dip antibacterial solution (rolling rate 70%, 40 *)! Drying (100*)! Tension
Process recipe
Prescription (g/L): Antibacterial Agent Herst ATB 40 Softener
Process analysis
Effect of the amount of antibacterial agent on the performance of antibacterial fabric
The amount of different antibacterial agents added will cause the fabric to have different antibacterial effects. Increasing the amount of antibacterial agent can enhance the antibacterial effect, but it will affect the physical properties of the fabric. Therefore, it is necessary to comprehensively consider the amount of antibacterial agent, the inhibition rate, and the cost, and select the best production process.
Effect of baking temperature time on antibacterial fabric
As can be seen from Table 3, 140 * is selected as the baking temperature for 0.5 min.
Antibacterial effect test
Main experimental equipment, equipment
Sterile laboratory; electrothermal pressure steam sterilization pot; electrothermal incubator; nutrient agar medium.
Test methods and strains
Method: AATCC100-1993 American AATCC standard strain: Escherichia coli (8099) 4.5+105 cfu/mL Staphylococcus aureus (ATCC6538) 4.8×105 cfu/mL Candida albicans (ATCC10231) 4.2×
Test sample
Antimicrobial Herst ATB-finished fabrics and 90-times washed antibacterial finishing fabrics without antibacterial treatment of the same fabric as an experimental control

Bacteriostatic effect
Antibacterial finishing agent toxicity test
The antibacterial finishing agent Herst ATB was acutely toxic; the 5% antibacterial Herst ATB application solution was administered to 40% of Kunming standard mice with an empty stomach for 16 h, and the dose of the antibacterial finishing agent HerstATB was as high as 10000 mg/kg. The poisoning performance of the animals was observed every day, and the experiment was completed in seven days. Each group of experimental animals was planted throughout the experiment without any poisoning performance, and the diet and exercise were normal, and none of the animals died. According to the acute toxicity grading standard, the antibacterial finishing agent application liquid is an actual non-toxic substance. Table 2 Effect of different amounts of antibacterial agent on the performance of antibacterial fabrics Antibacterial agent dosage / (g / L - 1) 0 20 30 50 60 70 inhibition rate /% 0 99.9 99.9 99.9 99.9 99.9 Table 3 Different baking temperature time on antibacterial fabric Effect of performance Antibacterial rate /% 99,9 99,9 99,9 99,9 99,9 99,9 Baking temperature /- 100 120 130 140 150 160 Baking time / s 240 120 60 30 30 20 Table 4 Antibacterial effect of antibacterial finishing fabric
Test sample
Golden
staphylococcus
the large intestine
Bacillus
white
Candida
Antibacterial finishing fabric
Washing antibacterial finishing fabric 90 times
Volume 28, Issue 3
March
Skin irritation: The hairs on both sides of the spine of 10 Japanese large ear standard test rabbits were cut off, and the 5% antibacterial HerstATB application solution was applied to the gauze and applied to the exposed skin on the right side. After 24 hours, the skin at the application site was observed, and no irritations such as erythema and edema occurred. According to the skin irritation intensity grading standard, the antibacterial finishing agent application solution was non-irritating to the skin. (3) Eye irritation: The 5% antibacterial Herst ATB application solution was directly dripped into the right eye and left eye of the Japanese rabbit with standard test, passively closed for 5 s, then rinsed with saline, 24 After h observation, there was no abnormality in the eyes. According to the eye irritation intensity grading standard, the antiseptic Herst ATB application solution was non-irritating to the eyes.
Micronucleus test: The micronucleus test of mouse bone marrow polychromatic erythrocytes was carried out according to the test method of GB7919-87. The results showed that there was no significant difference in the incidence of micronucleus between the antibacterial Herst ATB sample group and the solvent control group. Mutagenicity.
in conclusion
At present, the antibacterial finishing technology of textiles has reached a mature stage, and the antibacterial finishing process has become a conventional finishing process. Antibacterial finishing fabrics are superior to antimicrobial fibers in terms of antimicrobial spectrum and durability. The practice of mass production of antibacterial cotton fabrics by many manufacturers using the antibacterial finishing agent Herst ATB proves that Herst ATB is easy to use and low in cost. The inspection of the authoritative testing institutions at home and abroad proves that the modified chitin-based antibacterial and deodorant finishing agent Herst ATB has high-efficiency and durable antibacterial and deodorizing effect, safe and environmentally friendly, and can meet the requirements of customers in various countries for the quality of antibacterial products, and is suitable for industrial production. Method: Adjust the position accuracy of the double cylinder in the system, and repair the inner casing piston to ensure flexible and light sliding.
Double cylinder has no second descent
The possible failure is that the second drop solenoid valve is de-energized when the cylinder first drops, which is not allowed. Cause: The electromagnet (5TD) control program has a problem. Remedy: Check the control procedures for electrical operation.
Cylinder and hydraulic components leak a large amount of oil at the same time
Possible failure is that the oil grade is incorrect or the oil temperature is too high. Causes: First, the viscosity of the oil is low, the cohesive force between the molecules is small, and the leakage at the seal is increased. Second, the oil temperature is too high to lower the viscosity of the oil. Remedy: Accurately select the hydraulic oil brand number (usually select No. 68 hydraulic oil, North recommended "low condensation 68" hydraulic oil); control oil temperature, keep the oil cooler working normally.
Accumulator application
The accumulator acts as a pressure retaining force in the system. In the hydraulic system of the flat screen printing machine, the accumulator acts in the lifting circuit. At work, if the screw pump is turned off after starting, as long as the power supply is continuous, the original working pressure can still be maintained in the lifting circuit system. The shell of the accumulator is made of seamless steel pipe, which is filled with a pear-shaped skin capsule which is pressed with a nitrile rubber and an inflatable valve seat, and is divided into two chambers, one of which is filled with hydraulic oil and the inside of the skin. It is then filled with nitrogen. When the hydraulic fluid enters the accumulator, the bladder deforms and the volume of the gas decreases with increasing pressure, which causes the hydraulic fluid to be stored. If the system has pressure loss and needs to increase the hydraulic oil, the accumulator can absorb the rapid pressure pulse, which has good shock absorption and stable pressure. It also has the advantage of preserving the gas for a long time. The accumulator must be filled with nitrogen, which is an inert gas and is safe, rust-proof and prevents aging of the bladder. Note when inflating: (1) Remove the inflation valve guard on the rear of the accumulator
Rotate the handle on the inflatable tool with the head counterclockwise to the head, then to the end of the accumulator, the inflatable tool rubber
Pipe connection to nitrogen bottle
The operator stands on the side of the inflation valve connector and slowly opens the nitrogen cylinder valve.
Rotate the handle of the inflation tool clockwise and slowly fill it with nitrogen to make the endothelium of the accumulator expand slowly until the valve is closed, and the inflation speed can be increased. When the pressure on the watch reaches 1.8 mPa, control Hold the handle and keep this pressure for a few minutes to stabilize the pressure
The handle is reversed to the head, the inflation is stopped, and the nitrogen bottle is closed, and the inflation tool is removed.
After checking for any deflation, firmly install the inflation valve cover.
At present, the flat screen printing machine guide belt tends to double servo electric drive, and the distribution situation of the large-run hydraulically driven flat screen printing machine is similar to the above, for reference.
[China Antibacterial Fabric Network ]
ZeroClipboard.setMoviePath('/plugin/copytofriends/ZeroClipboard.swf'); var clip = new ZeroClipboard.Client(); clip.setHandCursor(true); clip.setText(" Fabric Antibacterial and Deodorant Finishing Practice http://www. 1kangjun.com/post585/"); clip.addEventListener('complete', function(client,text){ alert("Successfully copy this article to the clipboard!"); }); clip.glue('copytofriends');
Soccer Tracksuit,Sports Jacket,Suit Jacket,Running Tracksuit
Guangzhou LIDONG Garment Industry Co., Ltd. , http://www.lidongsports.com